Offshore Wind Data Acquisition SystemsΒΆ
Offshore wind farms are growing in complexity and size, expanding deeper into maritime environments to capture stronger and steadier wind energy. The intricacies of maritime environments such as unpredictable weather patterns and the long distance from shore make manual monitoring and maintenance a logistic challenge and economically draining. Data acquisition systems are deployed in offshore wind farms where the distance between Wind Turbine Generators (WTGs) and the offshore substation up to tens of kms while the distance between offshore substations and onshore substations or the mainland control room is up to hundreds of kms.
These Supervisory Control and Data Acquisition (SCADA) systems are the "nerve center" for large-scale offshore wind farms, collecting data from WTGs, offshore digital substation components, and meteorological stations [1]. These systems are vital for overseeing and controlling wind farm operations, offering comprehensive monitoring, control, and reporting functions. They accurately log events, improve the precision of alarm and event records, and reduce troubleshooting time. Offshore wind farm developers and operators often procure SCADA systems from WTG manufacturers who also serve as SCADA suppliers. These suppliers retain administrative control to support and manage system upgrades, which is essential for meeting the Service Level Agreements (SLAs) during the operation and maintenance phase following the commissioning of the offshore wind farm.
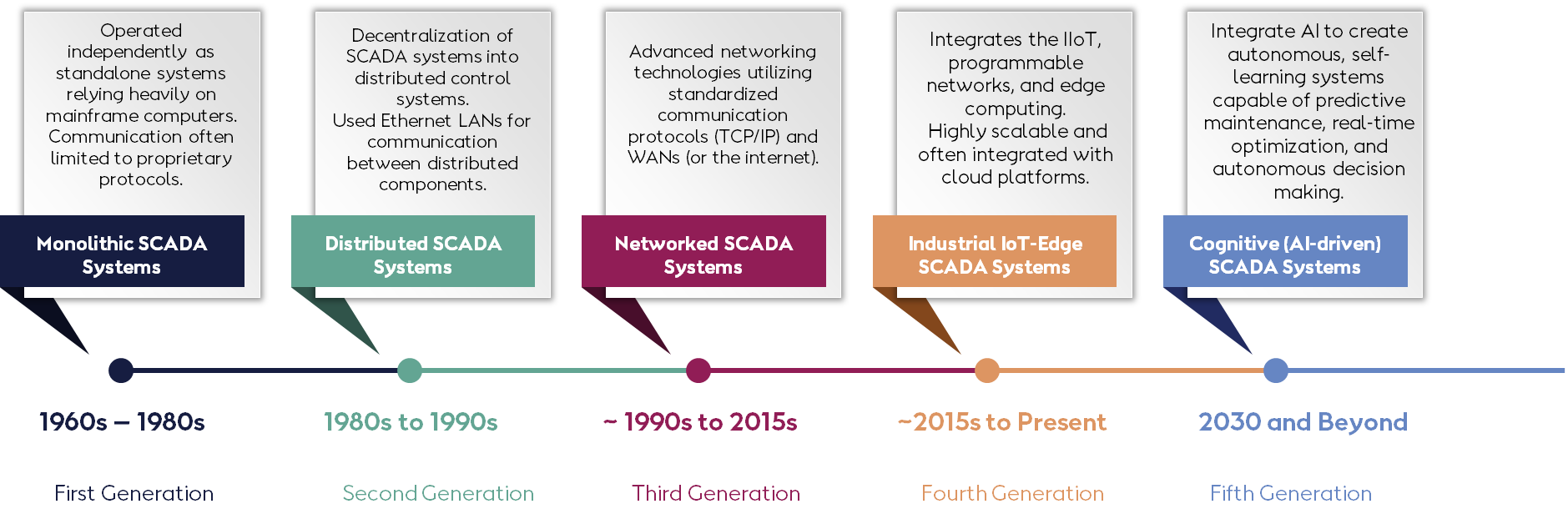
Data acquisition systems have come a long way. At the inception, monolithic SCADA systems (1960 -1980s) operated independently as standalone units relying heavily on mainframe computing. In this generation, the communication was limited to proprietary protocols which restricted interoperability.
The next generation (1980s -1990s) marked the decentralization of SCADA systems into distributed SCADA systems that facilitated distributed industrial control systems. With the advent of the internet, these SCADA systems used Ethernet LANs which facilitated communication between different components increasing system flexibility and scalability. In the third generation, advanced networking technologies such as standardized communication protocols like TCP/IP and WANs (or the internet) facilitated more extensive and integrated Networked SCADA systems.
Presently, we are seeing a gradual uptake of Industry 4.0 technologies such as Industrial Internet of Things (IIoT), Edge computing, and software-defined networking (SDN) supporting vast networks of sensors for big data collection from critical offshore infrastructure (assets). Some of the key drivers are (1) improved operational efficiency, (2) enhanced data analytics and decision-making, (3) and increased reliability through predictive maintenance. Further, these IIoT-Edge SCADA systems are highly scalable, and often integrated with cloud platforms, offering more dynamic and responsive operational capabilities. Lastly, adopting these technologies leads to reduced Operational Expenses (OPEX) and compliance with regulatory requirements and grid integration as there is highly granular and real-time data available.
In the future, we shall incorporate Artificial Intelligence (AI) to create autonomous, self-learning Cognitive (AI-driven) SCADA systems capable of predictive maintenance, real-time optimization, and autonomous decision making, significantly enhancing the efficiency and intelligence of industrial operations [2].